A breakthrough in crude oil processing could drastically reduce global CO2 emissions by up to 90%, as MIT engineers develop a novel filtration membrane using interfacial polymerization.
Separating crude oil into products such as gasoline, diesel, and heating oil is an energy-intensive process that accounts for about 6 percent of the world’s CO2 emissions. Most of that energy goes into the heat needed to separate the components by their boiling point.
Current Challenges in Crude Oil Separation
The conventional heat-driven process for fractionating crude oil makes up about 1 percent of global energy use, and it has been estimated that using membranes for crude oil separation could reduce the amount of energy needed by about ’90 percent’ . However, most efforts to develop a filtration membrane for hydrocarbons have focused on polymers of intrinsic microporosity (PIMs), including one known as PIM-1.
A New Approach: Interfacial Polymerization
MIT engineers have developed a new approach using interfacial polymerization, which has been widely used to create membranes for water desalination. The researchers modified the film by changing the bond that connects the monomers from an amide bond to an imine bond, allowing hydrocarbons to quickly move through the membrane without causing noticeable swelling of the film.
The Massachusetts Institute of Technology (MIT) is a private research university located in Cambridge, Massachusetts.
Founded in 1861, MIT is known for its science and technology programs, as well as its highly competitive admissions process.
The university has produced many notable alumni, including 98 Nobel laureates and 29 astronauts.
MIT's campus spans over 168 acres, featuring modern architecture and cutting-edge research facilities.
Key Innovation: Polyimine Membranes
The new filtration membrane can efficiently separate heavy and light components from oil, and it is resistant to the swelling that tends to occur with other types of oil separation membranes. The polyimine material has porosity that forms at the interface, and because of the cross-linking chemistry that was added in, you now have something that doesn’t swell.
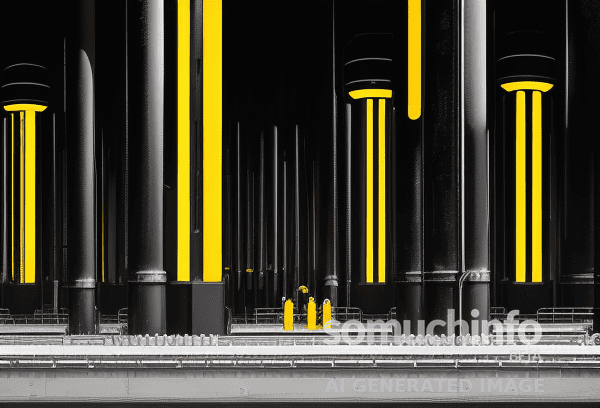
Potential Applications
The researchers believe that this approach could be used to create a series of filters that could be used to generate a higher concentration of the desired products at each step, replacing traditional crude oil fractionation columns. This technology has the potential to significantly reduce industrial energy consumption and improve the efficiency of the oil separation process.
The crude oil separation process involves several steps to separate and refine the various components of crude oil.
The first step is desalting, which removes salt and other impurities from the oil.
Next, the oil is heated and mixed with a solvent to extract the lighter hydrocarbons.
The resulting mixture is then separated into fractions based on their boiling points, including gasoline, diesel fuel, jet fuel, and lubricating oils.
According to the US Energy Information Administration, in 2020, the global crude oil separation capacity was approximately 100 million barrels per day.
Future Directions
The researchers are optimistic about the potential of this new approach, saying ‘This work takes the workhorse technology of the membrane desalination industry, interfacial polymerization, and creates a new way to apply it to organic systems such as hydrocarbon feedstocks.’ They believe that this technology could be adapted for industrial use by adopting existing manufacturing processes.
Conclusion
The development of polyimine membranes offers a promising solution to reduce the energy consumption required for crude oil fractionation. By leveraging interfacial polymerization, MIT engineers have created a new approach that can efficiently separate heavy and light components from oil, with potential applications in reducing industrial energy consumption and improving the efficiency of the oil separation process.
Polyimide membranes are a type of synthetic membrane made from polyimide polymers.
These membranes have high thermal stability, mechanical strength, and chemical resistance, making them suitable for various industrial applications.
They are often used in gas separation processes, such as air purification and carbon dioxide capture.
Polyimide membranes can also be applied in water treatment, fuel cells, and biomedical devices due to their biocompatibility and durability.