Tariff costs are set to hit Apple’s bottom line by up to $900 million, as the company ramps up manufacturing in the US amid escalating trade tensions with China.
Tariff costs will add $900 million to Apple’s bottom line in the April-June quarter.
Apple CEO Tim Cook warned that tariffs could cost the iPhone maker $900 million in the current period, addressing mounting concerns over U.S.-China trade tensions. The company manufactures a large portion of its iPhones in China, making it vulnerable to escalating trade war between the US and China.
Shift in Manufacturing Strategy
The shift in manufacturing strategy is aimed at mitigating geopolitical risk. Cook emphasized that having everything in one location poses too much risk. To address this, Apple plans to expand several U.S. teams, source 19 billion chips from suppliers across a dozen states, and continue producing components like iPhone glass through American suppliers.
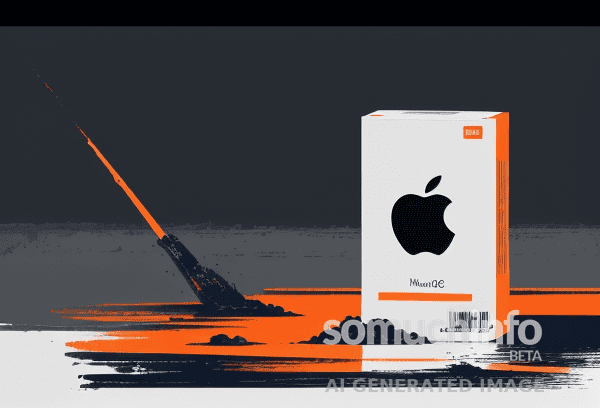
Over the next three months, Apple expects the ‘majority’ of U.S. iPhones to come from India, while Vietnam will be responsible for manufacturing ‘almost all’ U.S. iPads, Macs, Apple Watches, and AirPod products. China will remain the primary hub for Apple’s international production outside of the U.S.
Strong Q1 Results
Despite the uncertainty over tariffs, Apple posted strong results in all markets except China. Total revenue rose 5 percent year-over-year to $95.4 billion in the first three months of 2025, beating Wall Street expectations. iPhone sales reached $46.8 billion, up 2 percent from a year ago, while Mac and iPad sales climbed 7 percent and 15 percent, respectively.
Long-term Commitment to U.S. Manufacturing
Apple’s investments in U.S. manufacturing are part of its long-term commitment to supply chain resilience. The company has announced plans to spend $500 billion over the next five years on domestic initiatives, including a new facility in Houston focused on producing servers for AI.